Different Method Used In Small Maize Flour Mill Plant
Maize has been used for multiple purposes for centuries in the world, and mostly it is used as a food material; in some places it is used to feed the animal; in recent years, it is used for industry purposes: bio-ethanol(in biodiesel production). As bio-fuel technology requires a lot of investment and high technologies, it mostly happened in developed countries. For some developing countries like China, India, etc, the economic has been growing at a high level each year, population has been growing and the need for meat grows as a logical result. So poultry and livestock industry and the animal feed industry has developed to a new level compared with a couple of years ago.
Except for wheat flour, maize flour is the second largest grain product in the world, various of methods and maize flour mill plants are developed for processing maize flour product: wet milling method; dry milling method; dehulling and milling method.
The difference between wet milling method and dry milling method is that the former one requires the grits to be soaked in cold water for 2 hours and then dried for 12 hours in the drier at the temperature of 60 ℃, and then the milling part; with the 3rd method, 5% of water is added to the maize in the first place, then it’s manual pounding with the wooden pestle and mortar, then remove the light weighted materials and the brans, the left grits are milled in the similar method of wet milling.
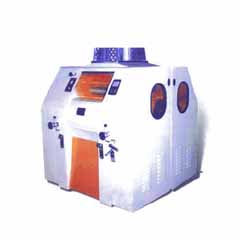
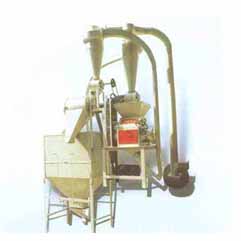