Flash Dryer
Drying is important for the proper preparation of materials prior to their briquetting. To make good quality briquette with high density, it is very important to control the moisture content of raw material to 8-12% before loading them into biomass briquette machine, so sawdust and other kinds of biomass need to be dried first.
Flash dryer is a pneumatic drying system used to dry products requiring the removal of free moisture. Flash dryers are using the heat from the airsteam.
Typical Applications of Flash Dryer
- Ideal for removal of moisture from free flowing materials which is light and small like sawdust, rice hull, milled stalks etc.
- suitable for small production scales below 700kgs per hour.
- Comparing with rotary dryer, the flash dryer has the advantages of low energy consumption and low cost. It is in simple design but have good effect as well.
- Suitable fuels for the boiler are wood waste, coal etc. The failed biomass charcoal can be fed into the boiler, too.
GC-DL series drying system
for Lower Moisture Content 20-25%
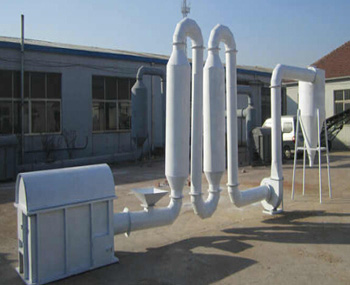
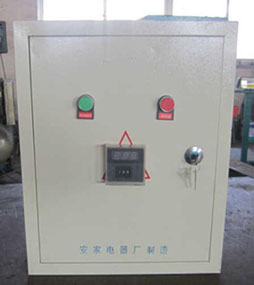
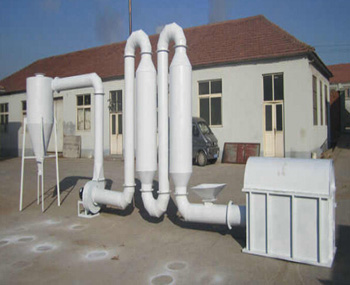
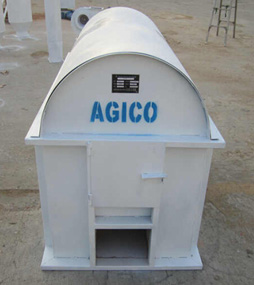
With a moisture reducing rate of 8-12%, the dryer GC-DL is equipped with a hot air boiler, which is suitable for drying raw materials with moisture content less than 20-25%.
Raw materials need to be dried if their moisture content is higher than mentioned above, and two or three time of dry up is necessary to achieve the demanded moisture content for wood briquette maker.
Model GC-DL-4, GC-DL-5.5, GC-DL-7.5
for biomass materials with lower moisture content 12-25%
In the biomass briquetting plant ,the moisture reducing rate of the dryer GC-DL-4, GC-DL-5.5, GC-DL-7.5 is 8-12%. This series of flash dryers are equipped with one hot air boiler, suitable for drying raw material with moisture content less than 20-25% for biomass briquetting.If the moisture content of the raw material for biomass briquetting is higher than that, it will need two or three times to dry to achieve the requested moisture content for biomass briquetting plant.
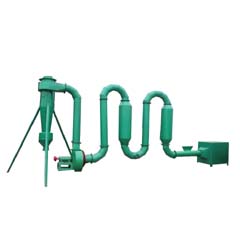
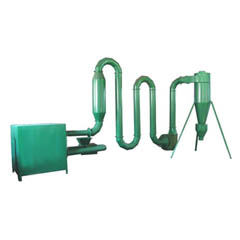
GC-DL Flash Dryer With One Boiler Stove
Model | GC-DL-4 Flash Dryer | GC-DL-5.5 Flash Dryer | GC-DL-7.5 Flash Dryer |
---|---|---|---|
Capacity(Kg/hour) | 200-250KG | 400-500KG | 500-700KG |
Size of Input Material(Diameter) | < 3mm & < 5mm | < 3mm & < 5mm | < 3mm & < 5mm |
Temperature of Hot Air | 180°C~250°C | 180°C~250°C | 180°C~250°C |
Consumption of Wood Waste | 15-20 kg/h | 25-30kg/h | 30-35kg/h |
Power(Centrifugal Fan+Air Lock) | 4kw+1.5kw | 5.5kw+1.5kw | 7.5kw+1.5kw |
Net/Gross Weight | 700/800kg | 1200/1300kg | 1800/1900kg |
Dimension(m) | 6×2×3.65m | 9×2×3.65m | 11×2×3.65m |
Twin boiler dryer model NHGJ-I, NHGJ-II, NHGJ-III for higher moisture content 20-50%
In the biomass briquette plant ,twin boiler dryer is a newly developed dryer with two hot air boilers, it is suitable for drying raw material with moisture content of 20% -50% for biomass briquetting. It can reduce moisture from 20%-50% to 8-12% for biomass briquetting only one passage or one time. PS: For raw material of moisture 20-35%, only fire and use the first boiler, no need to use the both.
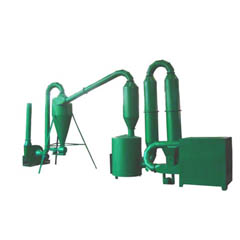
BHGJ Double Boiler Flash Dryer
Model | BHGJ-I Flash Dryer | BHGJ-II Flash Dryer | BHGJ-III Flash Dryer |
---|---|---|---|
Capacity(Kg/hour) | 200-250KG | 400-500KG | 500-700KG |
Size of Input Material(Diameter) | < 3mm & < 5mm | < 3mm & < 5mm | < 3mm & < 5mm |
Temperature of Hot Air | 180°C~250°C | 180°C~250°C | 180°C~250°C |
Consumption of Wood Waste | 40 kg/h | 60kg/h | 100kg/h |
Moister content max % | 20-50% | 20-50% | 20-50% |
Moisture of material after drying | 8-12% | 8-12% | 8-12% |
Power(Centrifugal Fan+Air Lock) | 5.5kw+1.5kw | 7.5kw+0.75kw | 11kw+0.75kw |
Net/Gross Weight | 700/800kg | 1200/1300kg | 1800/1900kg |
Overall dimension(L*W*H) | 9m*2m*4m | 9m*2.4m*4m | 9m*2.4m*4m |
Packing size | 9.2 M3(2 cases) | 14 M3(3 cases) | 14 M3(3 cases) |
Flash Dryer Performance Features
The whole system consists of fan blower, motor engine, fuel boiler, steel pipe, cyclone and air lock. In this system, wet material is input into hopper by screw feeder. Fuel furnace produces large volumn of hot air. Those hot air is driven into steel pipes, mixed with wet sawdust and moved through curving pipes and drying chamber by the power of fan blower. Fast moving hot air sustains and is mixed with raw material sent by spiral feeder in the suspending state through the steel pipe, moisture evaporates as the material traverses along the steel pipe and is rendered dry at teh discharge end. Humid air is continuously exhausted, thus the material is dried.
The air lock in the outlet stops the hot air to be exhausted to the atmosphere, but release the dried material via cyclone.
In the biomass briquetting plant, when wet raw material material is input into the hopper of dryer, the hot air stove (boiler) generates hot air, hot air mixed with wet sawdust and then sucked into the pipes by the exhaust blower(fan) , flowing and go though the curving pipes and drying chamber of dryer, thus the wet sawdust is dried, and the dried sawdust is discharged from the outlet with air lock.
In the biomass briquette plant, this type of dryer is suitable for drying heat sensitive material which is light and small like sawdust, rice shell, milled stalks etc. Generally wet material can be dried in a few minutes.Comparing with rotary dryer, it has the advantages of low energy comsumption, low cost, it’s in simple design but have good effect and high efficiency as well. In the biomass briquette plant ,the feeding of fuel for dryer boiler is by manual.The fuel can be wood waste like tree branch, tree trimmings, wood chips, coal or any waste that can burn (But Gas or Oil is impossible for the boiler now).
Flash Dryer Working Principle
The hot air enters into the bottom of the drier in tangent direction. Under the driving of the stirrer, a powerful rotating wind field is formed. The paste state materials enter into the drier through the screw charger. Under the powerful function of the sitting vanes at high-speed rotation, the materials are distributed under the function of strike, friction and shearing force. The block state materials will soon be smashed and contact the hot air fully and the materials are heated and dried. The dried materials after the de-watering will go up with the heat-air flow. The step rings will stop and keep the big particles. Small particles will be discharged out of the drier from the equipment by centrifugal force function and be smashed again after they fall down to the bottom.