Vegetable Oil Processing Plant
Pre-treatment
- Warm hulling process reduces energy consumption
- Double cracking and hulling process improve hulling ratio and reduce oil content in hull
- High volume hull bin makes the production flexible
- Making it possible to produce meals of various protein content (including meal milling)
- Adopt expansion process
- Auto-control
Pressing
Pre-pressing is a traditional method to process high oil-content oilseeds. Advantages of our pre-pressing technology are as follows:
- Versatile to process many oilseeds, such as rapeseed, cottonseed, sunflower seed and safflower seed, peanut, sesame etc.
- Complete with expansion process if required, which saves energy and high quality oil obtained at the same time
- Multi-stage filtration to the pre-pressed oil
- Less requirements to oilseeds quality
Solvent Extraction
We have developed two kinds of oil extraction process(rotor extraction and loop extraction). Till now, more than 10 oil extraction plants with working capacity over 1000MT have been built. Our oil extraction design, installation, and equipment are popular for less water, power, steam and solvent consumption; less oil residue in meal, top quality finished meal and crude oil.
Loop Extraction Process
- Rotation speed of Loop Extractor can be adjusted according to quantity of the incoming oil-bearing materials. In addition, constant material level in the above Buffer Tank avoids solvent leakage. It is negative pressure in the extractor, whcih reduces solvent leakage.
- Advanced miscella circulation will reduce fresh solvent use, reduce oil residue in meal, increase miscella concentration, and saves energy by reducing quantity of miscella entering into the evaporation system.
- Thin material layer in extractor ease percolation filtration. There is turnover at the bending part of Loop Extractor, which will reduce extraction corner. But this will cause too much meal in miscella. The meal should be removed before entering into the evaporation system.
Rotor Extraction
- Rotation speed of Rotor Extractor and Air Lock can be adjusted according to quantity of the incoming material. Keep constant material level in the above Buffer Tank make it easy to form negative pressure in the extractor and constant material level reduces solvent leakage.
- Advanced miscella circulation reduces fresh solvent use, reduce oil residue in meal, increase miscella concentration, and saves energy by reducing quantity of miscella entering into the evaporation system.
- High material level eases it to form immersion extraction and reduce the meal quantity in miscella. This will improve quality of crude oil and prevent against scaling in the evaporation system.
- Especially suitable for extraction of pressed cake
Degumming
Physical Refining
Remove gums in oil with special degumming method. FFA in oil is removed with steam. Features:
- high oil refining ratio, less oil loss;
- No waste water discharged;
- More FFA distilled out;
- Especially suitable for oils of high acid value, and low gum content;
Chemical Refining
Neutralize FFA in the oil with alkali. The gum and soap produced are centrifuges. Features:
- less requirements to crude oils;
- the finished oil is more consistent in quality;
- Less bleaching earth used compared with physical refining;
Bleaching
Add bleaching earth into the degummed oil. Under vacuum state, the oil is continuously mixed with bleaching earth in the Continuous Bleacher, where main part of colour bodies as well as oxidizing materials in the oil are absorbed by the bleaching earth. After Continuous Bleacher, the oil/clay mixture is passed through Leaf Filters where the spent earth is removed together with the precipitated materials from degumming. The oil then passes through one of two alternatively working safety filters before entering the next section.
Dewaxing / Winterizing
De-waxing system plays an important role in improving palatability, transparency and brightness of oils. The wax content is different in various oils. For maize oil, rice bran oil, sunflower seed oil, cottonseed oil etc. de-waxing is very important. The de-waxing methods are freezing, surface active agents, cold polymerizer, electrostatic, and winterizing etc. Currently winterizing method is most popular. The crystallizing temperature, crystallizing velocity, and crystal maturating time and filtering mode vary with oils.
Grain Silo
Silos are the necessary parts of oil plants. A well design silos will ensure the oilseeds to flow without interruption, safely with least cost. Facts of our silos:
- Deep-pit material discharging, special aspiration channel makes the material receiving clean
- Complete with dosing, cleaning and transferring devices
- Fluidized, uniform material discharging
- Frequency control make the material discharging easy to control and stable in working capacity
- Drying high-moisture materials
Finished Oil Packing Line
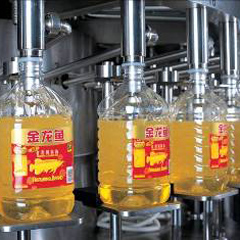
Finished Oil Filling Machine
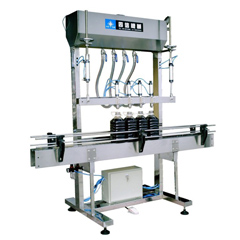
Finished Oil Filling Machine
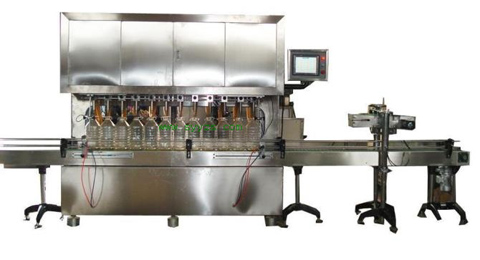
Finished Oil Packing Machine
Steam Boiler
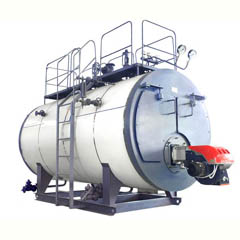
Typical Type: Down-Flow ,Fully Wet Back,Three-Pass Shell Boiler
- Oil(Gas)Fired Steam Boiler is of the type three-pass with wet back and central back-flame in the seriesl steam output more than 1T/H,flame tubes are symmetrical on furnance axis,uniform distribution is good to improve the stress of the Tube plates,fully wet back structure combustion chanmber inundates water completely so cooling conditions is good and back tube plates will not be scoured by the high-temp smoke,so the boiler running conditions and durability can be improved.
- The application of corrugated furnance not only increase the heating area but also lessened the damnification to buring chamber because of expansion on heating and contracting on cooling,Big volume furnance leads to completely buring and can save fuel.
- Front flame box fit by gemel,which can bring much convenience to open.After it is opened the furnance and flame tubes can be approached to clean and maintain.What’s more,big volunm furnance design can reduce the temperature of front flame box to avoid being damaged.
- Big steam space reduces the speed of the steam seperating from the surface of the water.The inner water separator set can insure high quality steam output.
- Blow down automatically:The blow down valve is controled according to the concentration of boiler ,it will be opened when concentration reach to the blow down values,normally,it will be closed.(The acts above will run automatically when the boiler is stopping) so it can save labour more and lessen the waste of water and fuel,slower the form of fur-scale efficiently in the boiler,and extend the life of boiler.
- Package construction and main auxiliary pre-assembled considerably reduce installation costs.
- Boiler can be operated completely by just using the fingers to press keys in the intelligentize digital control system
- Perfect protection:over-pressure switch on interlocking protection device,controllers giving alarms,burner stopped,blow down automatically with safety valves oppenning.
- Convenient maintenance: there is a access on top of the boiler for cleaning and maintenance if it’s needed.
- All of the boilers are tested with rated load in order to ensure the performance and reliability of burner,automatical controlling apparatus and rated security units.
- (0.8Mpa and smaller series with function of automatical blow down and fur-scale detecting)
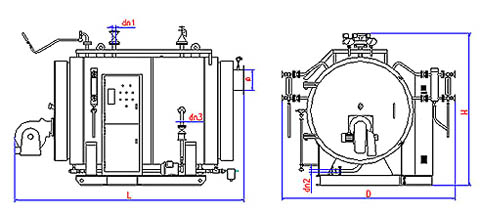
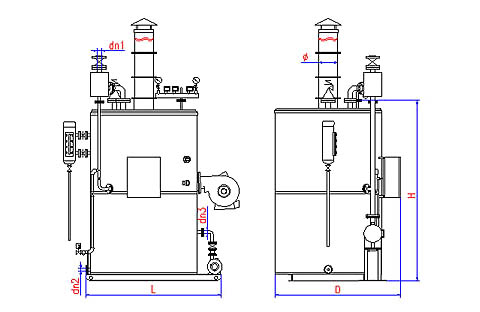
Oil Storage Tanks
The Oil storage tank we produced is suitable for the vegetable oils, gasoline, diesel oil and other oils with specific gravity of less than 1g/cm3 sand without apparent corrosive properties.It Has advantages of low construction cost, small land area, large storage capacity, safe and reliable operation, long service life, easy for management.
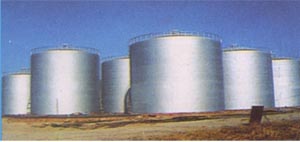
Storage Capacity Per Tank: from 50M3 to 5000M3